After graduating from college, Evan Shanks knew that his true calling reached far beyond a routine desk job. In 2012, he took a leap of faith and started his career as an automotive YouTuber, with a goal of becoming a positive influence while showcasing the ups and downs of building and modifying cars.
Today, Shanks is widely known by nearly one million fans across his social media platforms as a self-made mechanic, car enthusiast, YouTube influencer, and even as the owner of an athleisure company named Five Three Supply.
He’s a busy professional, and with that comes a regular requirements to maintain and enhance the infrastructure needed to support those types of diverse projects.
Showstopping Piece of Art
After nearly a decade of building his brand and follower base, Shanks’ platform had reached new heights at the start of this decade, and he wanted to continue that momentum while taking another step within his career. He had come to realize that his lack of home space to work on cars was a major problem, and that led to Shanks becoming somewhat resistant to new opportunities and business ventures.
To fix this, Shanks decided to find a new house with enough land to build his dream car shop. After moving into a new Texas home and spending months of methodically planning out and designing what his new shop would look like — later dubbed the “ShankShack” — construction began in late 2020. In addition to building and fabricating cars in this shop, Shanks’ plan was to install a welding station, hydraulic press, and engine building station.
For such a facility, Shanks needed something more durable and customizable than epoxy flooring. As such, he turned to coatings manufacturer LATICRETE after researching the potential benefits of the company’s SPARTACOTE resinous and decorative flooring system.
“Evan and Victoria [his wife] were amazing to work with,” said Jon Shelton, technical sales representative at LATICRETE. “They were super excited about this project from the beginning.”
With a polyaspartic system in mind, LATICRETE turned to Matt Johnson, then-general manager of Fort Worth, Texas-based Business Flooring Specialists (BFS), based on his team’s knowledge of the line and their past installation experience. With the intense wear-and-tear this shop would go through, Shanks needed a reliable applicator to install 3,200 square feet (297.3 m2) of flooring with performance properties that could stand up to the abuse his work entails.
“The polyaspartic allows for enhanced traction and durability compared to an epoxy, which is what Evan initially wanted,” Johnson said. “The tailored SPARTACOTE system is seamless, safe, highly durable, and easy to clean, and it reduces downtime by using innovative, quick return-to-service products.”
For what eventually became the ShankShack, technical features were only part of the equation for the contractor to consider. Decorative properties were critical, as well.
“Evan and his team wanted this floor to be more of a showstopping piece of art, unlike anything else in the garage floor sector,” Johnson recalled. “They wanted a custom glow flake design. Fortunately, LATICRETE’s variety of available textures, finishes, and colors allows us to match any decor, which enabled us to put together a glow-in-the-dark, custom chip blend.”
‘ShankShack’ Solution
Once Johnson and his six-person BFS team arrived at the Texas jobsite, they noticed the concrete was not completely flat and had some cracks. To address this, crew members needed to level the substrate to mitigate the possibility of future problems.
“The substrate was a smooth troweled concrete,” said Johnson, whose crew prepared the surface on day one of a four-day project. “It was in good condition. Fairly standard for troweled concrete, with small cracks to fill.”
Before filling any cracks, the floor was shot blasted with BlastPro BP9SP shot blasters — utilizing steel shot with attached Ermator S36 vacuums — to achieve the International Concrete Repair Institute’s (ICRI) concrete surface profile (CSP) 3 standard. Once blasted, the cracks and spalls were addressed with SPARTACOTE FAST FIX, a two-part, hybrid urethane crack repair material. Finally, the floor was evened out using Metabo 5-inch (12.7 cm) hand grinders.
“We marked all of the areas to be repaired with blue painters tape, since the Fast Fix sets up so fast,” said LATICRETE’s Shelton. “We would mix a few ounces at a time, and then run from spot to spot filling the areas.”
Once all flooring areas were level and smooth for the main coating application, a white coat of VAPOR BAN ER was applied as the basecoat. With material pulled using 12-mil (304.8 microns) Seymour Midwest rake squeegees and 3/8-inch (1.0 cm) nap rollers, the VAPOR BAN ER is described as a fast-curing, moisture mitigation primer. According to the manufacturer, it was designed to save time and money for installers.
Once the primer was applied and sanded down, the design was laid out, and each color was applied to the SPARTACOTE FLEX XPL. Again using rake squeegees and nap rollers, crew members applied the clear topcoat at approximately 10 mils (254.0 microns) wet film thickness (WFT). That set the stage for the chip design, which went underneath each lift while incorporating a custom blend of red, white, and black flakes.
“Because of the price of the flake, we pulled a clear coat to broadcast into and used the XPL with 100-grit mesh in the topcoat to ensure grip, even in wet environments,” said Johnson, whose crew wore gloves and spiked shoes as part of its personal protective equipment (PPE).
The glow-in-the-dark blends were applied to designated areas around the garage, with each outlined by a thick metallic black line to further illuminate the design. Once the custom chips were scraped down, the BFS team poured out the clear topcoat with traction additives.
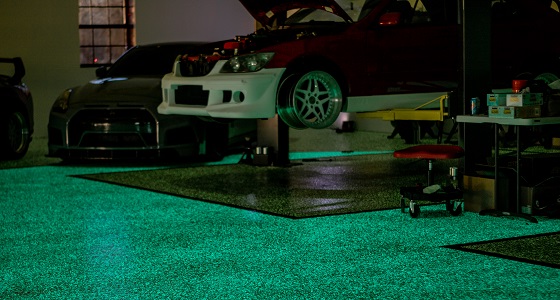
“Typically, most jobs involve applying custom flakes,” Johnson said. “Contractors would broadcast them into a basecoat, which usually results in losing flakes. Here, we broadcast the custom glow flakes into a thick clear coat to add more depth and give the finished project a unique appearance.”
The FLEX XPL polyaspartic offers high-solids content, minimal odor, and is low in volatile organic compounds (VOCs), according to the manufacturer. With both decorative and protective benefits, the system’s clear topcoat sealer features ultraviolet (UV)-resistant properties to prevent discoloration. Once applied, the two-part coating is ready for foot traffic within four hours, and it can handle vehicular traffic (necessary in Shanks’ garage!) after 24 hours.
When used with LATICRETE’s GRIP traction additive, the system provides optimal impact, abrasion, and chemical resistance, making it convenient for high-traffic applications.
Something to Show Off
Once the four-day project was complete, Shanks was able to move into the ShankShack and get back to his true passion — without a lack of space holding him back. That dream car shop had indeed become a reality.
“This
project showed how you could take what was going to be a nice place — regardless
of the type of flooring he put down — and turned it into a cool show piece that
was totally unique,” said LATICRETE’s Shelton. “It was a great way to take what
would be an everyday floor and make it something to talk about and show off.”
Since moving into his custom shop in late 2020, Shanks has recorded more than 60 YouTube videos and has reached nearly one million fans when utilizing this space to create content.
“I could not envision being more excited about a floor, from the custom designs to the finishing details and custom chip set,” said Shanks, who was impressed enough to bring back the same contractor and manufacturer for another job the next year.
“Since the beginning, these guys have been so enthusiastic and so involved,” Shanks said of team members with both the contractor and manufacturer. “They were the ones who were talking about wanting to do something cool and special for the ShankShack. They got it done!”